Le verre a une longue histoire dans le développement de l'humanité. Pour nous, le verre est l'un des matériaux les plus incroyables et les plus utiles, il a été utilisé dans tous les domaines de l'humanité. En même temps, nous savons aussi que le verre est un matériau fabriqué par l'homme.
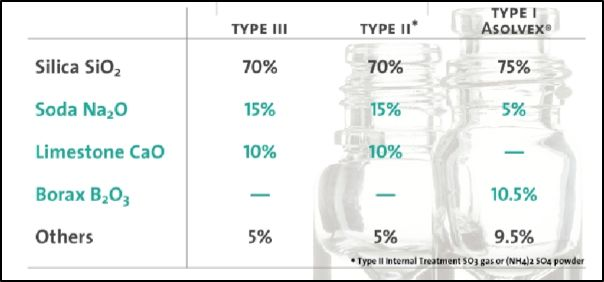
Le verre creux peut être utilisé dans de nombreux domaines, et nous le divisons en trois catégories : Type I, Type II et Type III.
Les types de verre se distinguent en fonction de la composition du verre et du traitement de la surface interne.
Leurs différences sont dues aux différents systèmes de composition du verre utilisés. Le verre de type I est un verre borosilicaté, les types II et III sont des verres de silicate sodocalcique. En ce qui concerne les types II et III, le type II est principalement basé sur le type III et utilise de la poudre de SO3 ou de NH4SO4 pour désalcaliniser la surface intérieure de la bouteille. (Note : Le but du traitement de désalcalinisation est principalement d'améliorer la résistance à l'eau des bouteilles en verre afin qu'elles puissent contenir des injections neutres ou faiblement alcalines).
Pour les emballages cosmétiques en verre, le verre de type III est principalement utilisé car le contenu des cosmétiques est moins corrosif pour le verre.
Composition des matières premières du verre sodocalcique
Les principales matières premières du verre sont le sable, le carbonate de soude, la calcite et le feldspath, qui représentent plus de 98% des matières premières du verre. Les autres petits ingrédients comprennent les clarificateurs, les colorants, les agents de décoloration, etc. En outre, grâce à la capacité puissante du verre, afin de recycler le verre et de réduire la consommation d'énergie, nous utilisons également le calcin comme l'une de nos principales matières premières (généralement de l'ordre de 0%-50%, parfois même 100%). C'est pourquoi nous disons que le verre est un matériau respectueux de l'environnement.
Le tableau ci-dessous montre clairement la fonction de chaque matière première.
Principales fonctions des matières premières et leur rôle dans la fusion du verre
Processus de fusion du verre sodocalcique
- Préparation des matériaux du lot
La salle de dosage place les matières premières du verre dans différents silos en fonction des besoins avant que le mélange n'entre dans le four. Les étapes du processus sont illustrées dans la figure :
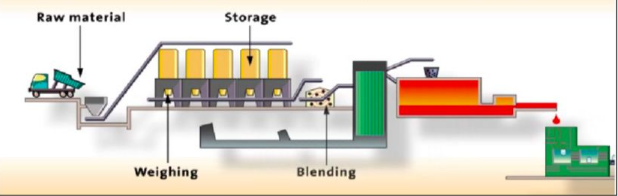
processus de fusion
Étape 1 : Transport des matières premières par train ou par camion jusqu'à la salle de dosage du verre, et vérification de la conformité de la taille et de la composition par une inspection visuelle et des tests sur des échantillons.
Étape 2 : Les matières premières sont placées à leurs points de déchargement respectifs, puis transportées vers la salle de dosage par des ascenseurs, et enfin transportées vers leurs silos respectifs.
Étape 3 : Avant d'entrer dans le four, les matières premières passent par les balances électroniques situées sous leurs silos respectifs et sont mises en lots et dosées.
Étape 4 : En règle générale, les matières premières sont pesées une par une et avec une grande précision d'un lot à l'autre.
Étape 5 : La sensibilité de la balance est contrôlée quotidiennement et étalonnée chaque semaine pour en garantir la précision.
Étape 6 : Une fois le pesage terminé, les matières premières sont acheminées vers le mélangeur.
Étape 7 : Dans certaines usines, le calcin est ajouté après le mélange afin de minimiser l'usure du calcin sur le mélangeur.
Étape 8 : Le mélange est transporté vers le four par des bandes horizontales ou des monorails.
Étape 9 : Afin de réduire la poussière, la stratification et les matériaux volants pendant le processus de transmission, une humidité appropriée est souvent ajoutée avant le mélange.
Étape 10 : Le matériau humide permet de mieux contrôler le dosage dans le four, ce qui est très bénéfique pour une fusion efficace.
- Processus de fusion
Le mélange est ajouté en continu au four par l'intermédiaire d'un alimentateur.
-~100°C : Le mélange est sec (~humidité d'environ 4%).
-~700°C : réaction en phase solide entre les carbonates
A partir de 800°C : élimination des carbonates et réaction avec la silice (environ 16% en poids)
A partir de 850°C : réduction du sulfate et de l'oxyde de fer par le carbone
A partir de 1200°C, la clarification s'accompagne d'une dissolution et d'une expansion de la silice
Dans l'industrie des récipients en verre sodocalcique, il existe deux principaux types de fours : les fours à flamme en fer à cheval et les fours à flamme croisée. L'image ci-dessous montre la structure du four régénérateur à flamme en fer à cheval.
Poêle en fer à cheval
Ce type de four comporte deux petits fours, côte à côte sur la paroi arrière du four, et le régénérateur est situé à l'arrière du four. Chaque petit four est équipé de 2 à 4 pistolets de chauffe. Ces canons de chauffe peuvent utiliser différents combustibles, tels que l'huile lourde et le gaz naturel, en fonction de la taille du four. La flamme sort du petit four d'un côté, puis tourne à 180° et sort de l'autre petit four. Le chemin emprunté par les flammes et les gaz d'échappement ressemble à un "U" horizontal. Cette conception permet au gaz de combustion d'avoir un temps de séjour relativement long dans le four, ce qui permet d'économiser de l'énergie.
Ce four est également équipé d'un système de préchauffage de l'air de combustion, que l'on appelle souvent régénérateur. Les régénérateurs permettent de réutiliser l'énergie thermique des gaz d'échappement brûlés. L'un des deux régénérateurs absorbe la chaleur des gaz de combustion (environ 1300°C), ce qui permet de chauffer le matériau réfractaire de la grille dans le régénérateur. L'air de combustion entre dans le four par un autre régénérateur. Après un certain temps, le flux d'air de combustion et de gaz de combustion s'inverse. L'air de combustion traverse le régénérateur qui vient d'être chauffé par les gaz d'échappement et pénètre dans le four. La chaleur stockée dans la grille est transférée à l'air de combustion pour le chauffer. Grâce à l'échange de chaleur comme les matériaux réfractaires, l'énergie peut être économisée et réutilisée.
- Canal d'alimentation utilisé pour transporter le verre fondu vers la machine de formage
Généralement, la température du verre à la sortie du four est trop élevée pour permettre le formage du verre d'emballage. C'est pourquoi le verre en fusion s'écoule d'abord dans le canal d'écoulement du matériau réfractaire, que nous appelons canal d'alimentation (voir l'image ci-dessous). La fonction du canal d'alimentation est de refroidir le verre jusqu'à la température de travail et en même temps d'uniformiser la température du verre refroidi.
Un des styles de conception du canal d'alimentation
Dans le canal d'alimentation, le verre présentant une bonne uniformité thermique est découpé en paraisons par le système de ciseaux, puis entre dans la machine de formage, pour finalement être transformé en verre en forme de bouteille.
Moulage
Le processus de formage des bouteilles et des pots en verre fait référence à une série de combinaisons d'actions (y compris le contrôle mécanique, électronique, etc.) qui sont répétées dans une séquence de programmation donnée, dans le but de produire une bouteille et un pot avec une forme spécifique attendue.
Il existe actuellement deux procédés principaux pour la production de bouteilles et de pots en verre : la méthode de soufflage pour les bouteilles à goulot étroit et la méthode de soufflage sous pression pour les bouteilles et les pots de plus grand diamètre.
Méthode de soufflage
Méthode du coup de bélier
Dans ces deux procédés de moulage, le verre liquide en fusion est coupé par une lame de cisaillement à la température du matériau (1 050-1 200 °C) pour former des gouttelettes de verre cylindriques, appelées "gobs". Le poids est suffisant pour produire une bouteille. Les deux procédés commencent par le cisaillement du verre liquide. Les gouttelettes tombent sous l'action de la gravité et passent à travers l'auge et l'auge de retournement dans le pré-moule. Le pré-moule est ensuite fermé hermétiquement et retiré par le haut par l'auge. La "tête volumineuse" est utilisée pour le scellement.
Processus de formation initiale du moule
Au cours du processus de soufflage, le verre est d'abord poussé vers le bas par l'air comprimé passant par la cloison, de sorte que le verre est formé au niveau de la filière ; ensuite, le noyau se déplace légèrement vers le bas, et l'air comprimé passant par l'espace dans la position du noyau se dilate de bas en haut. Le verre extrudé remplit le pré-moule. Grâce à ce soufflage, le verre prend une forme préfabriquée creuse, qui est ensuite soufflée à nouveau par de l'air comprimé dans une deuxième étape pour obtenir la forme finale.
Diagramme du processus de formation des bouteilles en verre
La production de bouteilles et de bocaux en verre se déroule en deux étapes principales : au cours de la première étape, tous les détails du moule du goulot sont formés et le goulot est achevé, y compris l'ouverture intérieure, mais la forme principale du produit en verre sera beaucoup plus petite que sa taille finale. Ces produits en verre semi-formés sont appelés "parisons" et sont ensuite soufflés pour obtenir la forme finale de la bouteille ou du bocal.
Schéma du processus de moulage par soufflage sous pression
Du point de vue de l'action mécanique, la matrice et le noyau forment un espace fermé en dessous. Une fois la matrice remplie de verre (après la fin du gazage), le noyau est légèrement rétracté, ce qui a pour effet de ramollir légèrement le verre en contact avec le noyau. Ensuite, l'air comprimé de bas en haut (air de soufflage) passe par l'espace sous le noyau pour former la paraison. Ensuite, la cloison se soulève, le pré-moule est ouvert et le bras de basculement, avec la matrice et la paraison, est basculé du côté du moule.
Lorsque le bras de retournement atteint le sommet du moule, les moules des deux côtés sont fermés et serrés pour envelopper la paraison. Le moule s'ouvre légèrement pour libérer la paraison, puis le bras de basculement retourne du côté du moule primaire et attend la prochaine étape. La tête de soufflage est abaissée au sommet du moule de formage, l'air comprimé est versé dans la paraison par le milieu, et le verre extrudé se dilate vers le moule de formage pour former la forme finale de la bouteille et de la canette.
Dans le procédé de pressage-soufflage, la paraison n'est plus formée à l'aide d'air comprimé, mais par extrusion du verre à travers un noyau plus long dans l'espace fermé de la cavité du moule préliminaire. Le retournement ultérieur et le façonnage final sont conformes à la méthode de soufflage.
Les bouteilles suivantes seront démoulées à l'aide de pinces à bouteilles et placées sur la plaque d'arrêt des bouteilles avec de l'air de refroidissement de bas en haut, en attendant d'être transférées vers le processus de recuit.
machine à fabriquer des bouteilles
La machine à fabriquer des bouteilles est un équipement qui permet de fabriquer des bouteilles et des bocaux en verre.
D'une manière générale, la machine à fabriquer les bouteilles comprend les 19 opérations les plus élémentaires pour former une bouteille. Actuellement, la plupart des machines et mécanismes de fabrication de bouteilles sont actionnés par de l'air comprimé (haute pression 4,2 bars, basse pression 2,2 bars). L'appareil est contrôlé électroniquement par un système de minuterie qui coordonne tous les mouvements.
Équipement de machine à fabriquer des bouteilles
La machine de fabrication de bouteilles la plus utilisée est la machine de fabrication de bouteilles à groupe individuel (machine IS). Cette machine comporte de 2 à 20 groupes identiques, dont chacun contient un ensemble complet de mécanismes pour répondre aux besoins de la production de bouteilles et de canettes. Tous les groupes de paraisons sont introduits dans chaque groupe par l'intermédiaire d'une écope mobile appelée distributeur de paraisons. La machine à fabriquer des bouteilles peut produire une, deux, trois ou quatre bouteilles en même temps (appelées gouttes simples, doubles, triples et quadruples). Aujourd'hui, une machine à fabriquer des bouteilles à 6 gouttes a même été développée et mise en production avec succès. Dans le cas de paraisons multiples, les ciseaux coupent les paraisons en même temps et tombent dans le pré-moule en même temps.
recuit
En refroidissant, le verre se rétracte et se solidifie. Un refroidissement inégal ou rapide provoque des tensions dans le verre, qui peuvent le fragiliser ou le faire exploser. Le four de recuisson a pour fonction de chauffer les bouteilles et les pots en verre à environ 580°C, puis de les refroidir lentement afin de réduire les tensions générées lors du moulage du verre et de garantir la sécurité des récipients en verre. Ce processus de recuit dépend de l'épaisseur du verre et dure généralement de 20 à 60 minutes.