En el desarrollo de la humanidad, el vidrio tiene una larga historia. Para nosotros, el vidrio es uno de los materiales más increíbles y útiles, se ha utilizado en todos los campos de la humanidad. Al mismo tiempo, también sabemos que el vidrio es un material fabricado por el hombre.
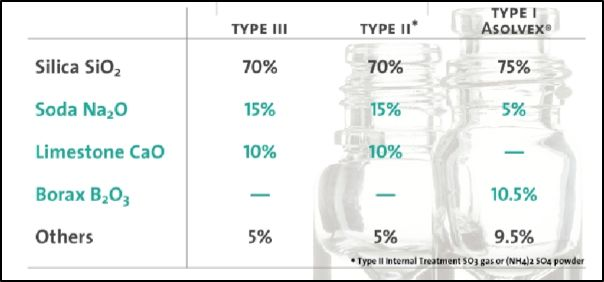
El vidrio hueco puede utilizarse en muchos campos diferentes, y lo dividimos en tres categorías: Tipo I, Tipo II y Tipo III.
Los tipos de vidrio se distinguen en función de su composición y del tratamiento de su superficie interna
Sus diferencias se deben a los distintos sistemas de composición del vidrio utilizados. El vidrio del Tipo I es de borosilicato, el de los Tipos II y III es de silicato sodocálcico. En cuanto al Tipo II y al Tipo III, el Tipo II se basa principalmente en el Tipo III, utilizando polvo de SO3 o NH4SO4 para desalcalinizar la superficie interior de la botella. (Nota: El objetivo del tratamiento de desalcalinización es principalmente mejorar la resistencia al agua de las botellas de vidrio para que sean adecuadas para contener inyecciones neutras a débilmente alcalinas).
Para los envases de vidrio de cosméticos, se utiliza principalmente el vidrio de Tipo III porque el contenido de los cosméticos presenta menos corrosión en el vidrio.
Composición de la materia prima del vidrio sodocálcico
Las principales materias primas del vidrio son la arena, la ceniza de sosa, la calcita y el feldespato, que representan más de 98% de las materias primas del vidrio. Otros pequeños ingredientes incluyen clarificantes, colorantes, agentes decolorantes, etc. Además, gracias a la poderosa capacidad del vidrio, con el fin de reciclar el vidrio y reducir el consumo de energía, también utilizamos cullet como una de nuestras principales materias primas (generalmente en el rango de 0%-50%, a veces incluso 100%,). Por eso decimos que el vidrio es un material respetuoso con el medio ambiente.
Podemos ver claramente la función de cada materia prima en la siguiente tabla
Principales funciones de las materias primas y su papel en la fusión del vidrio
Proceso de fusión del vidrio sodocálcico
- Preparación de los materiales del lote
La sala de dosificación coloca las materias primas de vidrio en diferentes silos en función de las necesidades antes de que la mezcla entre en el horno. Las etapas del proceso se muestran en la figura:
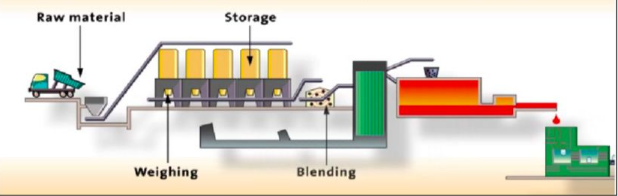
proceso de fusión
Paso 1: Transportar las materias primas a la sala de dosificación de vidrio en tren o camión, y garantizar el cumplimiento del tamaño y la composición mediante inspección visual y pruebas de muestras.
Paso 2: Las materias primas se colocan en sus respectivos puntos de descarga, luego se transportan a la sala de dosificación mediante ascensores y, por último, se transportan a sus respectivos silos.
Paso 3: Antes de entrar en el horno, las materias primas pasan por las básculas electrónicas situadas bajo sus respectivos silos y se dosifican y dosifican.
Paso 4: Normalmente, las materias primas se pesan de una en una y con precisión lote a lote.
Paso 5: La sensibilidad de la báscula se controla diariamente y se calibra cada semana para garantizar su precisión.
Paso 6: Una vez finalizado el pesaje, las materias primas se transportan a la mezcladora.
Paso 7: En algunas fábricas, el cascajo se añade después de la mezcla para minimizar el desgaste del cascajo en la mezcladora.
Etapa 8: La mezcla se transporta al horno mediante cintas horizontales o monorraíles.
Paso 9: Para reducir el polvo, la estratificación y los materiales voladores durante el proceso de transmisión, a menudo se añade la humedad adecuada antes de mezclar.
Paso 10: El material húmedo mejora el control de la dosificación en el horno, lo que es muy beneficioso para una fusión eficiente.
- Proceso de fusión
La mezcla se añade continuamente al horno a través de un alimentador.
-~100°C: La mezcla está seca (~la humedad es de unos 4%)
-~700°C: reacción en fase sólida entre carbonatos
A partir de 800°C: eliminación de carbonatos y reacción con sílice (aproximadamente 16% en peso)
A partir de 850°C: reducción del sulfato y del óxido de hierro por el carbono.
A partir de 1200°C, la clarificación va acompañada de la disolución y expansión de la sílice
En la industria de envases de vidrio sódico-cálcico-sílice, existen dos tipos principales de hornos, los hornos de llama de herradura y los hornos de llama cruzada. La siguiente imagen muestra la estructura del horno regenerador de llama de herradura.
Estufa de herradura
Este tipo de horno tiene dos hornos pequeños, uno al lado del otro en la pared trasera del horno, y el regenerador está situado en la parte trasera del horno. Cada pequeño horno está equipado con 2-4 pistolas de calentamiento. Estas pistolas de calentamiento pueden utilizar diferentes combustibles, como aceite pesado y gas natural, en función del tamaño del horno. La llama sale del horno pequeño por un lado, gira 180° y sale por el otro horno pequeño. La trayectoria que siguen las llamas y los gases de escape es como una "U" horizontal. Este diseño permite que el gas de combustión tenga un tiempo de residencia relativamente largo en el horno, con el consiguiente ahorro de energía.
Este horno también está equipado con un sistema de precalentamiento del aire de combustión, que es lo que solemos llamar regenerador. Los regeneradores permiten reutilizar la energía térmica de los gases de escape quemados. Uno de los dos regeneradores absorbe el calor de los gases de escape de la combustión (aproximadamente 1300°C), calentando así el material refractario de la parrilla del regenerador. El aire de combustión entra en el horno a través de otro regenerador. Al cabo de cierto tiempo, el flujo de aire de combustión y de gases de escape de la combustión invierte su dirección. El aire de combustión fluye a través del regenerador que acaba de ser calentado por los gases de escape y entra en el horno. El calor almacenado en la parrilla se transferirá al aire de combustión para calentarlo. Mediante el intercambio de calor como los materiales refractarios, la energía puede ahorrarse y reutilizarse.
- Canal de alimentación utilizado para transportar el vidrio fundido a la máquina de conformado
Normalmente, la temperatura del vidrio que sale del horno es demasiado alta para el moldeo de vidrio para envases. Por lo tanto, el vidrio fundido fluye primero hacia el canal de flujo de material refractario, que es lo que llamamos el canal de alimentación (véase la imagen de abajo). La función del canal de alimentación es enfriar el vidrio hasta la temperatura de trabajo y, al mismo tiempo, uniformizar la temperatura del vidrio enfriado.
Uno de los estilos de diseño del canal de alimentación
En el canal de alimentación, el vidrio con buena uniformidad térmica será cortado en trozos por el sistema de tijeras, y luego entrará en la máquina formadora, y finalmente formado en vidrio con forma de botella.
Moldeo
El proceso de conformado de botellas y tarros de vidrio se refiere a una serie de combinaciones de acciones (incluyendo el control mecánico, electrónico, etc.) que se repiten en una secuencia de programación determinada, con el objetivo de producir una botella y un tarro con una forma específica esperada.
En la actualidad existen dos procesos principales para la producción de botellas y tarros de vidrio: el método de soplado para botellas de boca estrecha y el método de soplado a presión para botellas y tarros de mayor diámetro.
Método de soplado
Método de soplado a presión
En estos dos procesos de moldeo, el líquido de vidrio fundido es cortado por una cuchilla de cizalla a su temperatura de material (1.050-1.200°C) para formar gotitas cilíndricas de vidrio, llamadas "gobs". El peso es suficiente para producir una botella. Ambos procesos parten del cizallamiento del líquido de vidrio. Las gotitas caen bajo la acción de la gravedad y pasan a través de la artesa y la artesa giratoria al molde preliminar. A continuación, el molde preliminar se cierra herméticamente y se extrae por la parte superior mediante la artesa. La "cabeza voluminosa" se utiliza para el sellado.
Proceso inicial de formación del molde
Durante el proceso de soplado, el vidrio es empujado primero hacia abajo por el aire comprimido que pasa a través del mamparo, de modo que se forma el vidrio en la matriz; a continuación, el núcleo se desplaza ligeramente hacia abajo, y el aire comprimido que pasa a través del hueco en la posición del núcleo se expande de abajo hacia arriba. El vidrio extruido llena el molde preliminar. Con este soplado, el vidrio se conforma en una forma prefabricada hueca, que posteriormente se vuelve a soplar con aire comprimido en una segunda etapa para obtener la forma final.
Diagrama del proceso de formación de botellas de vidrio
La producción de botellas y tarros de vidrio tiene lugar en dos etapas principales: en la primera se forman todos los detalles del molde de la boca y se completa la boca, incluida la abertura interior, pero la forma principal del producto de vidrio será mucho más pequeña que su tamaño final. Estos productos de vidrio semiformados se denominan parisones, y en el momento siguiente se soplan para darles la forma final de botella y tarro.
Diagrama esquemático del proceso de moldeo por soplado a presión
Desde el punto de vista de la acción mecánica, la matriz y el núcleo forman un espacio cerrado por debajo. Después de llenar la matriz con vidrio (una vez finalizado el gaseado), el núcleo se retrae ligeramente, lo que hace que el vidrio en contacto con el núcleo se ablande ligeramente. A continuación, el aire comprimido de abajo hacia arriba (aire de soplado posterior) pasa por el espacio bajo el núcleo para formar el parison. A continuación, el mamparo se eleva, el molde preliminar se abre y el brazo de volteo, junto con la matriz y el parison, se voltea hacia el lado del molde.
Cuando el brazo abatible alcance la parte superior del molde, los moldes de ambos lados se cerrarán y se sujetarán para envolver el parisón. El molde se abrirá ligeramente para liberar el parison; entonces el brazo de volteo volverá al lado del molde primario y esperará la siguiente ronda de acción. El cabezal de soplado se baja hasta la parte superior del molde de formación, se vierte aire comprimido en el parison desde el centro y el vidrio extruido se expande hacia el molde de formación para dar la forma final a la botella y la lata.
En el proceso de prensado-soplado, el parison ya no se forma utilizando aire comprimido, sino que se forma extruyendo vidrio a través de un núcleo más largo en el espacio cerrado de la cavidad del molde preliminar. El volteo posterior y la conformación final se corresponden con el método de soplado-soplado.
Las botellas siguientes se extraerán del molde con pinzas para botellas y se colocarán en la placa de parada de botellas con aire de refrigeración ascendente, a la espera de ser transferidas al proceso de recocido.
máquina para fabricar botellas
Las máquinas de fabricación de botellas son equipos que pueden fabricar botellas y tarros de vidrio.
En términos generales, la máquina de fabricación de botellas incluye las 19 operaciones de acción más básicas para formar una botella. En la actualidad, la mayoría de las máquinas y mecanismos de fabricación de botellas se accionan mediante aire comprimido (alta presión 4,2 bar, baja presión 2,2 bar). El dispositivo está controlado electrónicamente por un sistema de temporizador para coordinar todos los movimientos.
Equipos de fabricación de botellas
La máquina de fabricación de botellas más utilizada es la máquina de fabricación de botellas de grupo individual (máquina IS). Esta máquina tiene de 2 a 20 grupos idénticos, cada uno de los cuales contiene un conjunto completo de mecanismos para satisfacer las necesidades de la producción de botellas y latas. Todos los grupos de gobos se introducen en cada grupo a través de una cuchara móvil llamada distribuidor de gobos. La máquina de fabricación de botellas puede fabricar una, dos, tres o cuatro botellas al mismo tiempo (denominadas gotas simples, dobles, triples y cuádruples). En la actualidad, incluso se ha desarrollado y puesto en producción con éxito una máquina de 6 gotas. En el caso de las gotas múltiples, las tijeras cortan las gotas al mismo tiempo y caen en el molde preliminar al mismo tiempo.
recocido
Al enfriarse, el vidrio se contrae y se solidifica. El enfriamiento desigual y el enfriamiento rápido provocan tensiones en el vidrio, lo que puede hacer que se vuelva quebradizo o explote. La función del horno de recocido es calentar las botellas y tarros de vidrio hasta unos 580°C y, a continuación, enfriarlos lentamente para aliviar la tensión generada durante el moldeado del vidrio y garantizar la seguridad de los envases de vidrio. Este proceso de recocido depende del grosor del vidrio y suele durar entre 20 y 60 minutos.