In the world of packaging, ensuring that customers receive undamaged glass bottles is a critical aspect of maintaining brand reputation and customer satisfaction. Glass bottles, while often preferred for their aesthetic appeal and sustainability, are fragile and prone to breakage during transit. This blog post will delve into best practices for packaging, shipping, and handling glass bottles to minimize damage. We’ll explore various strategies that businesses can implement to protect their products, enhance customer experience, and ultimately drive sales.
Understanding the Importance of Packaging
The Role of Packaging in Customer Experience
Packaging plays a fundamental role in shaping customer perception and experience. When customers receive a product that is well-packaged, it not only protects the item but also conveys a sense of professionalism and care from the brand. In the case of glass bottles, the stakes are even higher. Customers expect the integrity of the product to be preserved, especially when they’re paying a premium price for beverages, cosmetics, or other goods. An undamaged bottle signals quality and reliability, fostering trust in the brand.
Conversely, receiving a damaged product can lead to disappointment and frustration. This negative experience can have far-reaching consequences, including lost sales, negative reviews, and damage to the brand’s reputation. Therefore, investing in effective packaging solutions is essential not only for protecting glass bottles but also for enhancing overall customer satisfaction. Businesses that prioritize packaging are more likely to cultivate loyal customers who return for future purchases.
The Impact of Breakage on Business
The financial implications of damaged glass bottles can be significant. Every broken bottle represents a loss of revenue, not only from the cost of the product itself but also from the shipping and handling expenses incurred. Additionally, businesses must consider the cost of returns and replacements, which can quickly add up. According to industry studies, product returns due to damage can account for a substantial percentage of operational costs, particularly in the e-commerce sector.
Moreover, the environmental impact of breakage should not be overlooked. Each broken bottle contributes to waste, and the need for replacements increases the carbon footprint associated with transportation and production. By taking proactive steps to minimize breakage, businesses can not only save money but also contribute to a more sustainable future.
Best Practices for Packaging Glass Bottles
Choosing the Right Packaging Materials
Selecting the appropriate packaging materials is the first step in ensuring glass bottles arrive undamaged. Businesses must consider using materials specifically designed for protecting fragile items. Here are some recommended materials:
- Cardboard Boxes: Sturdy cardboard boxes provide a solid outer layer of protection. Opt for double-walled boxes for added strength, especially for heavier bottles.
- Bubble Wrap: This classic packaging material is excellent for cushioning glass bottles. Wrap each bottle individually in bubble wrap, ensuring that all sides are covered. This will help absorb shock and prevent breakage from impacts during transit.
- Packing Peanuts: These lightweight materials can fill any gaps in the box, preventing bottles from shifting during transportation. Make sure to use biodegradable options to enhance sustainability.
- Foam Inserts: Custom foam inserts can be designed to snugly fit each bottle, providing superior protection. These inserts prevent movement and absorb shocks, making them ideal for high-end products.
- Dividers: Utilizing dividers within boxes can help separate individual bottles, reducing the risk of them colliding with one another. This is particularly useful when shipping multiple bottles at once.
Designing Effective Packaging Solutions
The design of the packaging is just as important as the materials used. Here are some tips for creating effective packaging solutions:
- Size Matters: Ensure that the box is appropriately sized for the bottles being shipped. A box that is too large can allow excessive movement, while a box that is too small can put pressure on the bottles, increasing the risk of breakage.
- Sealing the Package: Use high-quality packing tape to securely seal the boxes. Reinforcing the seams and edges with extra tape can provide additional strength, ensuring the package remains intact during transit.
- Labeling: Clearly label packages with “Fragile” stickers to alert handlers to exercise caution. Including handling instructions not only helps protect the product but also communicates the brand’s commitment to quality.
- Weight Distribution: When packing multiple bottles, distribute the weight evenly within the box. This not only helps prevent breakage but also makes handling easier for shipping carriers.
- Testing Packaging Solutions: Before finalizing packaging solutions, conduct drop tests to assess how well your packaging withstands impacts. This can provide valuable insights into potential weaknesses and allow for adjustments before mass production.
Shipping Best Practices
Choosing Reliable Shipping Partners
Selecting reliable shipping partners is essential for ensuring that glass bottles are handled with care throughout the transit process. Research potential shipping providers and consider their track record with fragile items. Look for carriers that offer specialized services for handling fragile goods, and ensure they have protocols in place for minimizing breakage.
It’s also beneficial to maintain open communication with shipping partners. Share your concerns about fragile items and inquire about their handling procedures. A shipping partner that understands the importance of protecting glass bottles will be more likely to prioritize careful handling and timely delivery.
Tracking Shipments
Implementing a robust tracking system allows businesses to monitor shipments and address any issues in real-time. Providing customers with tracking information enhances their experience by keeping them informed about the status of their orders. Additionally, tracking shipments can help identify patterns related to breakage or delays, enabling businesses to make data-driven decisions to improve packaging and shipping processes.
Offering Insurance Options
Consider offering shipping insurance for glass bottles, especially for high-value products. Insurance can provide peace of mind for both the business and the customer, ensuring that any potential losses due to breakage are covered. Clearly communicate the insurance options available at checkout, allowing customers to make informed decisions about their purchases.
Handling and Storage Considerations
Employee Training
Educating employees on proper handling techniques is crucial for minimizing breakage. Conduct training sessions that focus on the importance of gentle handling, especially when dealing with glass bottles. Employees should be trained to recognize the fragility of glass and understand how to properly lift, transport, and store bottles. Additionally, emphasize the importance of following packaging and shipping protocols to maintain consistency and quality.
Proper Storage Solutions
Implementing proper storage solutions within warehouses is essential for protecting glass bottles before they are shipped. Here are some best practices for storage:
- Shelving Systems: Utilize shelving systems that can accommodate glass bottles securely. Ensure that shelves are stable and not overcrowded, as excessive weight can lead to accidents.
- Temperature Control: Maintain a stable temperature in storage areas. Extreme temperatures can cause glass to expand or contract, increasing the risk of breakage.
- Organized Layout: Keep glass bottles organized and accessible. An organized layout reduces the chances of mishandling and makes it easier for employees to locate products.
Implementing Quality Control Measures
Incorporating quality control measures throughout the packaging and shipping process can significantly reduce the risk of damage. Establish checkpoints to inspect packaging materials, ensure proper sealing, and verify that handling procedures are followed. Regularly review and adjust quality control protocols based on feedback and data collected from shipping and customer service teams.
Customer Communication and Support
Setting Expectations
Clear communication with customers is essential for managing expectations regarding glass bottle deliveries. Provide detailed information about packaging and shipping processes on your website. Highlight your commitment to quality and the steps taken to ensure that products arrive undamaged. Transparency builds trust and reassures customers that their orders are in good hands.
Offering After-Sales Support
In the event that a customer does receive a damaged glass bottle, having an efficient after-sales support system in place is vital. Train customer service representatives to handle complaints with empathy and efficiency. Ensure that they are equipped to process returns or replacements swiftly, minimizing customer frustration. A positive resolution to a negative experience can turn a dissatisfied customer into a loyal advocate for your brand.
Gathering Customer Feedback
Encourage customers to provide feedback on their experiences with packaging and shipping. Utilize surveys or follow-up emails to gather insights on how well products were protected during transit. Analyzing this feedback can help identify areas for improvement and inform future packaging strategies.
Sustainability Considerations
Eco-Friendly Packaging Solutions
As consumers become increasingly environmentally conscious, opting for sustainable packaging solutions can enhance brand reputation and appeal. Consider using biodegradable packing materials, such as compostable peanuts or plant-based wraps. Additionally, explore the possibility of using recycled cardboard boxes to reduce environmental impact.
Promoting Reusability
Encourage customers to reuse glass bottles once they’ve consumed the product. Provide suggestions for repurposing bottles, such as using them for home decor or storage. This not only promotes sustainability but also fosters a deeper connection between customers and your brand, as they see value in reusing your products.
Conclusion
Ensuring that customers receive undamaged glass bottles is a multifaceted challenge that requires attention to detail at every stage of the packaging and shipping process. From selecting the right materials and designing effective packaging solutions to implementing best practices in shipping and handling, businesses must prioritize the protection of their products. By fostering a culture of quality and sustainability, brands can enhance customer satisfaction, build loyalty, and ultimately drive success in an increasingly competitive marketplace.
Investing in proper packaging and shipping strategies is not merely a cost; it is an investment in your brand’s reputation and customer relationships. By adopting the practices outlined in this guide, businesses can ensure that their glass bottles arrive safely, reinforcing their commitment to quality and care. As the market continues to evolve, those who prioritize customer experience through careful packaging will stand out, paving the way for long-term success.
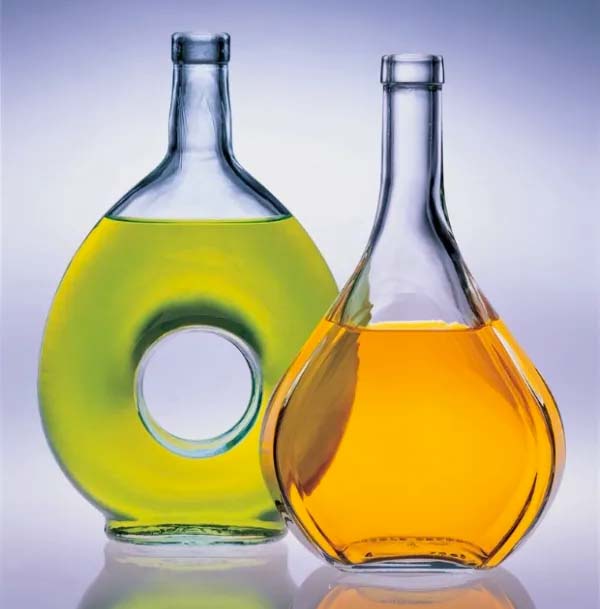