The delivery lead time for glass bottles is a crucial aspect of the supply chain process, impacting manufacturing schedules, inventory management, and customer satisfaction. In this comprehensive 1400-word exploration, we will delve into the factors influencing glass bottle delivery lead times, strategies to optimize lead time efficiency, and the importance of communication and collaboration between suppliers and customers in ensuring timely deliveries.
Understanding Glass Bottle Delivery Lead Time
Factors Influencing Lead Time
- Quantity Ordered: The volume of glass bottles ordered significantly affects lead times. Larger quantities may require longer production and processing times.
- Customization Requirements: Customized glass bottles, with unique designs, colors, shapes, or branding, often entail longer lead times due to the additional manufacturing steps involved.
- Supplier Location: The geographical location of the glass bottle supplier impacts lead times, especially when considering transportation and shipping durations.
- Production Capacity: The production capacity of the supplier plays a key role in determining lead times. Higher capacities can potentially reduce lead times.
- Demand and Seasonality: Fluctuations in demand and seasonal variations can impact lead times, especially during peak periods.
Typical Lead Time Estimates
- Stock Bottles: For standard, non-customized glass bottles readily available in stock, lead times can range from a few days to a week.
- Custom Orders: Custom glass bottles may require lead times ranging from a few weeks to a couple of months, depending on the complexity of the customization.
- Large Orders: Bulk orders typically have longer lead times due to the scale of production, ranging from a few weeks to several months.
- International Orders: Importing glass bottles from overseas suppliers may involve longer lead times due to shipping, customs clearance, and potential transit delays. Strategies to Optimize Glass Bottle Delivery Lead Time
1.Effective Communication
- Clear Requirements: Provide detailed and accurate specifications to suppliers to avoid misunderstandings and delays.
- Regular Updates: Maintain open communication channels with suppliers to stay informed about order progress and potential delays.
- Streamlined Production Processes
-Lean Manufacturing: Implement lean principles to eliminate waste, improve efficiency, and reduce production lead times.
- Batch Production: Opt for batch production to streamline processes and optimize production schedules.
- Inventory Management
Forecasting: Use demand forecasting techniques to anticipate customer needs and adjust inventory levels accordingly to minimize lead times.
Safety Stock: Maintain adequate safety stock levels to mitigate supply chain disruptions and unexpected demand spikes.
- Supplier Relationship Management
Partnership Approach: Foster strong relationships with glass bottle suppliers based on trust, collaboration, and mutual understanding to enhance lead time reliability.
- Supplier Performance Evaluation: Regularly assess supplier performance to identify areas for improvement and ensure timely deliveries.
- Technology Integration
Supply Chain Software: Implement supply chain management software to enhance visibility, track orders, and optimize production and delivery processes.
Automation: Integrate automation technologies to streamline production, reduce manual errors, and expedite order processing.
Importance of Timely Glass Bottle Deliveries
- Customer Satisfaction : Timely deliveries enhance customer satisfaction, build trust, and foster long-term relationships with clients.
- Inventory Management**: Minimizing lead times reduces inventory holding costs, prevents stockouts, and improves overall inventory management efficiency.
- Operational Efficiency: Efficient lead times optimize production schedules, reduce bottlenecks, and enhance operational efficiency.
- Competitive Advantage: Timely deliveries give businesses a competitive edge, positioning them as reliable suppliers in the market.
Conclusion
In conclusion, the delivery lead time for glass bottles is a critical aspect of the supply chain that requires careful planning, effective communication, and collaboration between suppliers and customers. By understanding the factors influencing lead times, implementing strategies to optimize efficiency, and recognizing the importance of timely deliveries, businesses can enhance customer satisfaction, improve operational efficiency, and gain a competitive advantage in the market. By prioritizing lead time optimization and fostering strong supplier relationships, organizations can streamline their supply chain processes and achieve greater success in the glass bottle industry.
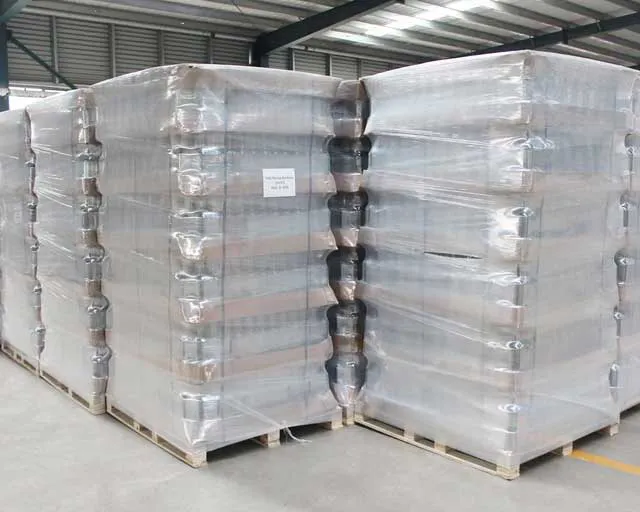