Glass bottle manufacturing background
As a traditional packaging container, glass bottles have a long history. Since ancient times, the glass bottle manufacturing industry has occupied a place in my country’s economic development. With the advancement of science and technology and the development of society, the glass bottle manufacturing industry is constantly undergoing technological innovation and industrial upgrading. At present, the glass bottle manufacturing industry has formed a complete industrial chain, including raw material supply, production and manufacturing, product testing and sales.
The importance of glass bottles in modern society
In various fields of modern society, glass bottles play an important role. First of all, in the food and beverage industry, glass bottles are widely used to package alcohol, beverages, condiments, etc. due to their non-toxic, hygienic, and transparent characteristics. Secondly, in the pharmaceutical industry, glass bottles have the advantages of corrosion resistance, high temperature resistance, and good sealing, which provide safety guarantee for the storage and transportation of medicines. In addition, in the daily necessities industry, glass bottles are also favored by consumers because of their beautiful and practical features.
Research purpose and significance
Aiming at the key technical issues in the glass bottle manufacturing process, this study aims to explore the optimization of the glass bottle manufacturing process, the control of key factors, and performance testing and quality control methods. Through in-depth research, it provides theoretical guidance and practical reference for improving the technical level and product quality of my country’s glass bottle manufacturing industry. In addition, this study will also focus on the application of environmental protection and sustainable development in glass bottle manufacturing, with a view to providing useful reference for the green development of the industry. In short, this research is of great significance for promoting the scientific and technological progress and industrial upgrading of my country’s glass bottle manufacturing industry.
Glass bottle manufacturing process
Selection and processing of glass raw materials: The manufacturing of glass bottles first stems from the selection of high-quality raw materials. Usually, the main raw materials of glass bottles include quartz sand, soda stone, limestone, etc. When selecting raw materials, the quality must be strictly controlled to ensure that the purity and particle size of the raw materials meet specified standards. In addition, the ratio of raw materials is also very critical. A reasonable ratio can improve the physical properties and chemical stability of glass bottles. In the process of processing raw materials, the raw materials need to be pre-processed such as drying and grinding to ensure the smooth progress of the melting process.
Glass melting and homogenization: After pretreatment, the raw materials enter the melting furnace for melting. During the melting process, temperature and time control are crucial. The melting temperature is usually around 1500°C to ensure that the raw materials are fully melted. The molten glass needs to be homogenized to eliminate defects such as uneven composition and bubbles. The homogenization process is usually carried out at a slightly lower temperature, and the components of the glass liquid are made uniform by slow stirring.
Glass forming process:
Blowing method: Blowing method is a traditional glass forming process. During the blowing process, workers use a blowpipe to blow molten glass into the desired shape. The blowing method is highly flexible and adaptable and is suitable for producing glass bottles of various shapes and sizes.
Mold forming method: Mold forming method is a process that uses metal molds to manufacture glass bottles. Pour the molten glass liquid into the mold, and after cooling and solidification, a glass bottle of the desired shape is obtained. The mold forming method is suitable for mass production and has high production efficiency, but the mold cost is high.
Vacuum blister method: Vacuum blister method is a relatively advanced glass molding process. By forming a vacuum on the mold, the molten glass liquid is adsorbed on the mold under the action of vacuum suction, thereby forming the desired glass bottle shape. This process has the advantages of fast molding speed and good surface quality.
Annealing and cooling of glass bottles: Glass bottles need to be annealed after forming to eliminate internal stress and prevent the bottle from bursting. The annealing process is carried out in a special annealing furnace, and the temperature gradually decreases to slowly cool the glass bottle. The annealed glass bottle has high strength and stability, making it easy for subsequent processing and use. During the cooling process, the cooling rate must be controlled to avoid thermal stress and affect the quality of the glass bottle.Key factors in the glass bottle manufacturing process
Temperature control: In the glass bottle manufacturing process, temperature control is a crucial factor. The precise control of temperature directly affects the melting, forming and cooling processes of glass. Temperatures that are too high or too low can cause quality problems in glass bottles. In the melting stage, it is necessary to ensure that the glass raw material is fully melted and reaches the required melting temperature; in the molding stage, the temperature of the glass frit must be controlled to maintain its good fluidity and molding performance; in the annealing and cooling stages, reasonable temperature control It can eliminate the stress inside the glass and prevent the bottle from exploding.
Gas pressure control: In the glass bottle manufacturing process, gas pressure control is also critical. Especially in molding processes such as blowing and vacuum molding, the stability of gas pressure has an important impact on the shape, size and wall thickness of glass bottles. Too high or too low gas pressure will cause problems such as local uneven thickness and deformation of glass bottles. Therefore, during the production process, an advanced gas pressure control system needs to be used to ensure pressure stability and improve product quality.
Molding speed and cooling speed: Molding speed and cooling speed are important factors affecting the quality of glass bottles. If the molding speed is too fast or too slow, it will affect the shape, size and internal structure of the glass bottle. The cooling rate is directly related to the stress distribution and internal defects of the glass bottle. Reasonable control of the molding speed and cooling speed will help improve the strength, impact resistance and heat of the glass bottle.
Surface quality and internal defects of glass bottle: The surface quality and internal defects of glass bottles have an important impact on their service life and safety performance. During the manufacturing process, factors such as raw materials, processes, and equipment should be strictly controlled to reduce defects such as surface scratches, bubbles, and stones. In addition, by optimizing the molding process and improving. Cooling methods the stress inside the glass bottle can be reduced and risks such as cracks and explosions can be reduced.
To sum up, in the glass bottle manufacturing process, temperature control, air pressure control, molding speed and cooling speed, as well as surface quality and internal defect are key factors. Only by strictly controlling these factors can we ensure the quality if glass bottle and meet the performance requirements of various industries for glass bottle.
Performance testing and quality control of glass bottle manufacturing
Physical property testing of glass bottles
Impact resistance: The impact resistance of glass bottles is one of the important indicators to measure their quality. During the testing process, methods such as the falling ball test and the pendulum impact test are usually used to evaluate the impact resistance of glass bottles. By testing the impact resistance of glass bottles, we can ensure that they are not easily broken during transportation, handling and use, thus ensuring the personal safety of consumers.
Heat resistance: The heat resistance of glass bottle refers to its stability and thermal shock resistance in high temperature environments. Detection methods mainly include high-temperature immersion test, thermal cycle test, etc. Through these tests, the risks of deformation and rupture of glass bottles in high-temperature environments can be evaluated to ensure their application safety in food, beverage and other industries.
Chemical corrosion resistance: Glass bottles may be exposed to various chemical substances during storage and transportation, such as acids, alkalis, salts, etc. Chemical corrosion resistance testing mainly includes immersion tests, titration tests, etc. to evaluate the stability and safety of glass bottles in different chemical environments.
Size and shape inspection of glass bottles: The accuracy of size and shape is crucial to the quality of glass bottles. During the production process, high-precision testing equipment such as optical measurement and three-coordinate measurement are used to detect the diameter, height, wall thickness and other dimensions of the glass bottles to ensure that they meet the design requirements. At the same time, the shape of the glass bottles is tested to avoid defects such as deformation and bending.
Surface quality inspection of glass bottles: Surface quality is directly related to the aesthetics and usage experience of glass bottles. Advanced technologies such as visual inspection and laser scanning are used to inspect the surface of glass bottles to find and eliminate surface defects such as bubbles, scratches, and stains.
Through the
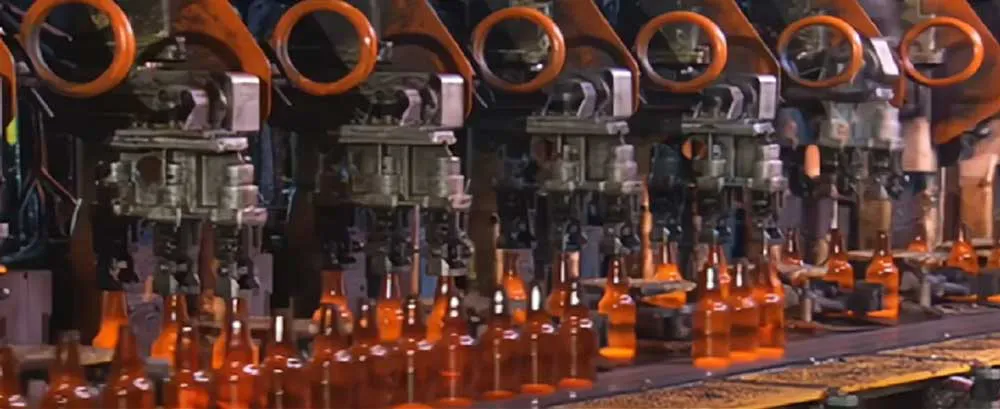