Glass bottle molds, also known as glass molds or glass formers, are typically made of cast iron or steel. These materials are chosen for their durability, heat resistance, and ability to withstand the high temperatures required in the glass manufacturing process. Here are some details about the materials commonly used for making glass bottle molds:
Cast Iron:
Cast iron is a common material used for making glass bottle molds due to its high heat resistance and durability. It can withstand the high temperatures of the glass manufacturing process without warping or deforming.
Steel:
Steel is another material often used for making glass molds. It is known for its strength and ability to maintain its shape under high heat conditions. Steel molds are durable and can be used repeatedly in the glass production process.
Ceramic Coatings:
In some cases, glass molds may have ceramic coatings to enhance their heat resistance and durability. These coatings help protect the mold surface and improve its longevity during the glass forming process.
Specialized Alloys:
Some glass bottle molds may be made from specialized alloys that offer specific properties suited for the glass manufacturing process. These alloys are designed to withstand the extreme conditions of glass production and ensure the quality and consistency of the formed glass bottles.
Precision Machining:
Glass bottle molds are typically precision-machined to ensure the accuracy and quality of the final glass products. The molds need to be carefully crafted to create the desired shape and dimensions of the glass bottles.
Overall, the choice of material for glass bottle molds is crucial to ensure the quality and consistency of the glass bottles produced. Cast iron, steel, ceramic coatings, and specialized alloys are commonly used materials that provide the necessary durability, heat resistance, and precision required for the glass manufacturing process.
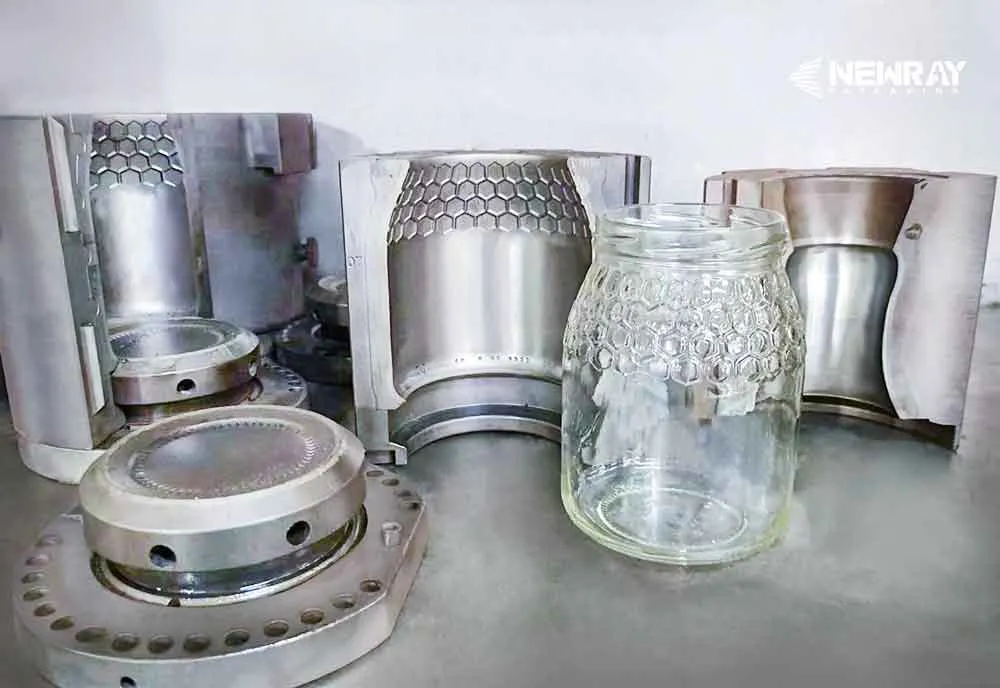